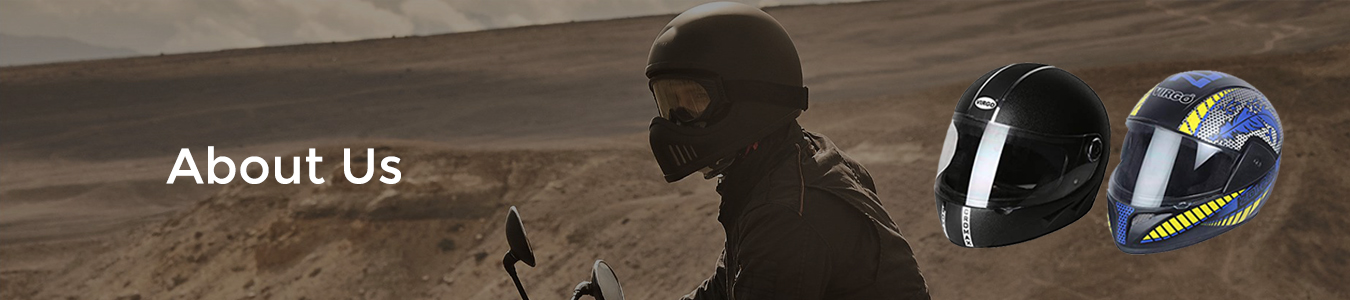
About Us
We offer a variety of different helmets to fit every need or every helmet we manufacture, including mirrored shields. For more than 18 years now, we have ensured that every rider has the proper protection. Safety should not be forgone due to a lack of affordability which is why we choose to keep our prices reasonable. Affordable Protection to all is more than a tagline for us.
As we enter our 19th year, the excitement is building here at Virgo No1 and Sapphire as we prepare to unveil our new line of helmets, Full face, Modular’s, Off road helmets, and a full line of kids helmets, its all being retooled. Just watch out ,it will be out VERY SOON!
R & D
We are driven by passion. Technicians, engineers and designers give their best to get the best from our helmets.
Infrastructure
Total Land Area : 10800 Square Feet
Manpower : 125 Trained Work Force
Paint Shop Capacity : 6000Pcs Per Day
Die Casting & Machine Combined : 1.8 Lks per Month.
Operational Since : 2000
Specialized Metalized in Power Coating Facilities.
In-house Corrugation Facilities.
We are driven by passion. Technicians, engineers and designers give their best to get the best from our helmets.
Specialized in-house Graphic Designing & Printing Facilities.
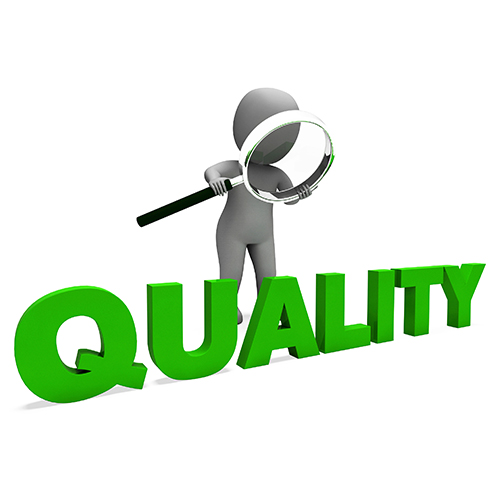
Quality Control
A certain number of our helmets are always retained as we batch test every model in our test laboratory. Each helmet is looked at in minute detail to ensure that quality and safety are paramount. We also verify that each model meets or exceeds the test standard required by its country of destination. This may be BIS (IS 4151 : 2015). Numerous tests are undertaken on the EPS and the external shell for shock absorption. We also test the fit as many testing houses now take this into account. always
Precision Assembly
A certain number of our helmets are always retained as we batch test every model in our test laboratory. Each helmet is looked at in minute detail to ensure that quality and safety are paramount. We also verify that each model meets or exceeds the test standard required by its country of destination. This may be BIS (IS 4151 : 2015). Numerous tests are undertaken on the EPS and the external shell for shock absorption. We also test the fit as many testing houses now take this into account. always
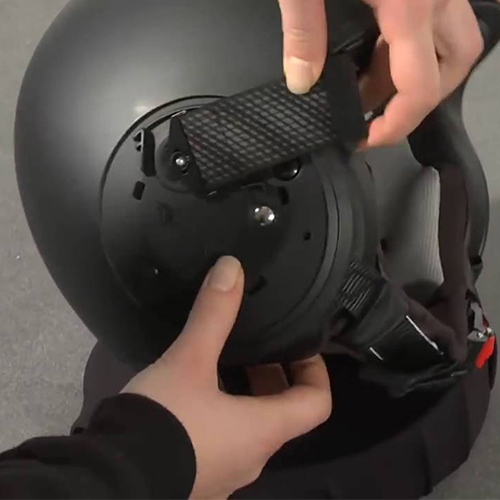
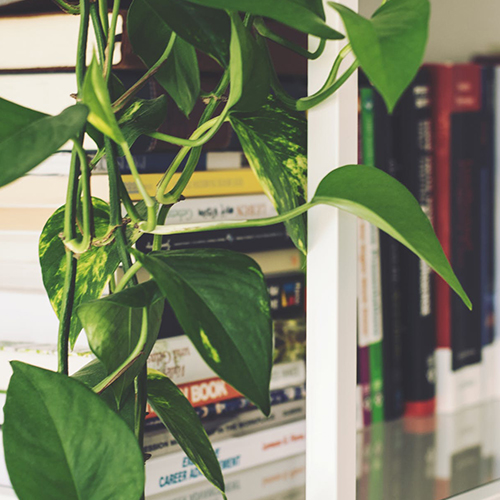
In House Knowledge
Once a shell has been removed from its mould it is checked to make sure it meets our exacting standards by our technical experts. Several layers of paint and the graphics are applied, the helmet is lacquered with anti UV and the process gives a unique touch to each helmet.